Custom Projects
The ANA New Way examined batch manufacturing and made Recipe writing simple and flexible, avoiding the pitfalls of pseudo-automation that requires operators to manually press icons for each step. New Way approaches made ordinary process measurements into virtual analyzers by judiciously selecting combinations of parameters to add new information – not just numbers. And, of course, this same strategy went further, addressing time, more specifically how to compress it so the old way of travel can be supplanted by the New Way of Cloud communication.
Every one of these solutions came about because ANA saw – or was told! – that there is a need. Everything ANA does routinely now, was once someone’s wish.
Let us put that know-how to work on your tough-but-vital problem. Here are two examples that show how the core competencies ANA has developed in batch automation, together with the skill set ANA brings to the table, solve tough problems.
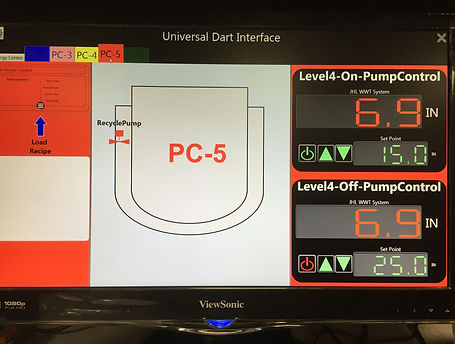
Project 1 - Specialty Chemicals Manufacturer
Problem: Refresh and modernize a dependable idea whose hardware is aging rapidly. The customer had a continuous process wastewater treatment system that had been custom engineered to exacting specifications many years ago. This project was made more challenging since the key controller needed to be replaced; the process could not be allowed to go off-line for more than a few hours before the new one would kick in; and all the prior specifications needed to be met rigorously at a minimum.
ANA’s solution modularized the continuous process, breaking it down into a series of steps, on each of which ANA imposed a traceability standard. Exactly what came in and what left needed to be known and recorded. As can be seen, there is a clear element of the DART batch methodology inside this solution. The result was an in-spec, modern, reliable replacement at a price that was a fraction of what a brand new installation would have cost.

Project 2 – Food Additives Manufacturer
Problem: A high-demand, profitable food additive was not being made fast enough to satisfy demand. The rate-limiting step was the particle size that needed to be able to be adjusted both quickly and predictably. Grinding too little always resulted in a need for re-work. Grinding too much was time intensive, producing no real benefit but costing more to manufacture.
ANA’s solution was to automate the speed with which raw material was fed, using an algorithm keyed to the speed of the drive. The result was a 25% increase in speed, and a project that paid for itself in a few weeks.